Let me start with this and if you take anything away from this The Lightning Class story, it is the story of Corinthian sail racing, innovative development and open to all.
Double planking and the Skaneateles Boat Co.
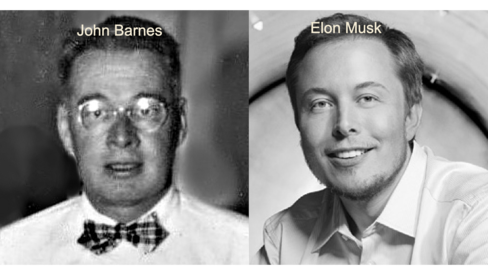
Yes, I can make this case...
We live in a time of great advancement and change. Times that favor young folks that can see the world from a different perspective, Mr. Musk is the embodiment of this, a fresh approach... AT SCALE.
John Barnes lived at such a time, Henry Ford was piling iron ore on one end of a giant factory and Model T's drove out of the other end... at prices middle America could afford. AT SCALE.
Apply it to wooden boat building? Well it happened when young Barnes was coming of age. And it was done applying new science, in this case it was Jefferies No. 2 Glue, a foul British concoction imported here by L.W. Ferdinand and Co. Boston Mass.
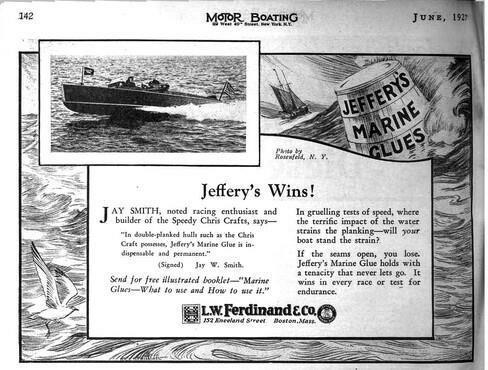
The problem with manufacturing boats at scale in a modern factory in the 1920s-30s is that they were made of wood, and the part in the water, the bottom planking, was the issue.
So a bit of time on the problem.
Wood is a wonderful engineering material and if well cared for will last in a boat for centuries... USS Constitution? (she got Jefferies too in her '28 rebuild).
Wood when wet moves. In carvel planking like the Lightning was designed for it must be planned for in construction AND IN SUBSEQUENT CARE.
Primmer:
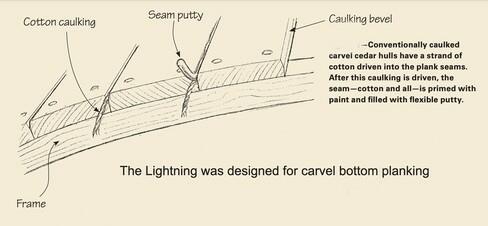
A strong building method, the plank edges are carefully shaped to receive a hard (cotton) caulking material, carefully tapped into the seams just enough that the hull "rings" like a dull drum but no more, the water will do the rest. This makes the hull watertight when the water "swells" the wood fibers. The putty is for appearance and smoothness.
The essential fact here that most DIY'ers miss is that the first time a plank swells it "edge sets"... FOREVER... When a new wooden boat is stored for the season she will dry out and the seams will open. If not fooled with, they will "take up" to the original "set" next season. Used to be common knowledge. With the advent of 'Goos and Potents" it was reflexive to "caulk the seams" So when the boat goes overboard the planks try to return to the original set and the fibers are crushed. Uh oh... Now we have a leaker.
So back to manufacturing, for the general public we have a problem. Buy a new car and it should start up and go immediately, so it follows if you buy a new boat it should immediately float.
Enter Chris Craft, a favorite up on Henderson Harbor in the Twenties.
Christopher Columbus Smith's children in the Twenties could see the possibilities of mass production AT SCALE for the new middle class market if they could solve the planking problem. When they did, production leaped from dad's one boat every week or two to 900 in the year before the Depression.
How? change from carvel to batten seam top side planking and most important a double planked bottom with a layer of cotton soaked with Jefferys Glue in between... floats immediately.
The Chris Craft factory in the Twenties, from the left the inner planking is covered with cotton fabric and soaked with Jefferys Glue and to the right the outer planking is beddied in the glue. (the fabric is easily seen at the transom).
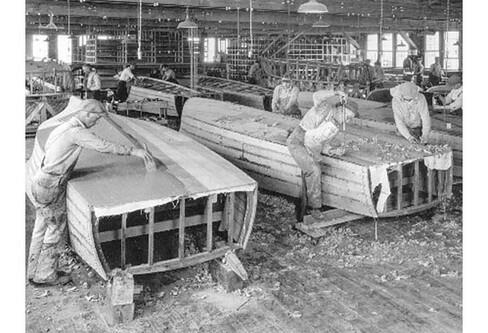
And the glue itself? You still can get it from Davies in England. The schooner people in Maine today swear by it for tight deck seams.
And foul? The stuff is made from 1 part natural rubber (latex) dissolved in 12 parts naphtha (petroleum) and heated to 300 degrees and blended with 22 parts of shellac which is made from the secreatment of dead bugs, Laccifer lacca...
Comes in a box and you have to heat it back up to 300 degrees to pour it.
Yuck...
There you have it. In the Forties The Hubert Johnson Lightnings were built in this fashion with a double planked bottom of a 45 degree herringbone pattern inner planking, glue and cotton fabric, and fore and aft planking on the outside.
Next up: what did Barnes do at Skaneateles to build sailboats AT SCALE for the very first time? Look for Part 2 to be posted soon.